7 outils Lean Manufacturing pour une optimisation des processus
La méthode 5S
C’est une méthode d’organisation japonaise basée sur cinq grands principes, visant à l’amélioration continue de l’environnement de travail pour gagner en efficacité et en productivité.
5S 5 verbes d'action japonais (Seiri,Seiton,Seiso,Seiketsu,Shitsuke)
S1: Seiri-Débarrasser : Ce qui n'est pas utilisé régulièrement est rangé, voire jeté.
S2: Seiton-Ranger: chaque chose à une place bien définie.
S3: Seiso-Nettoyer :Le nettoyage permet d'éviter des dysfonctionnements pour ce qui concerne les biens de production, sécurise les lieux et rend le cadre de travail sein
S4: Seiketsu-Maintenir l'ordre: Une fois que tout est trié, rangé et nettoyé, il convient de maintenir ce nouvel ordre.
S5: Shitsuke-Etre rigoureux : Cette méthode n'est efficace que si ses préceptes illustrés par les 4S précédents sont respectés. C'est le sens de ce 5ème S.
L’approche DMAIC :
Le modèle DMAIC est une approche structurée de résolution de problèmes. Cet outil simple permet d’obtenir rapidement des résultats probants, et repose sur 5 étapes : Define, Measure, Analyse, Improve et Control
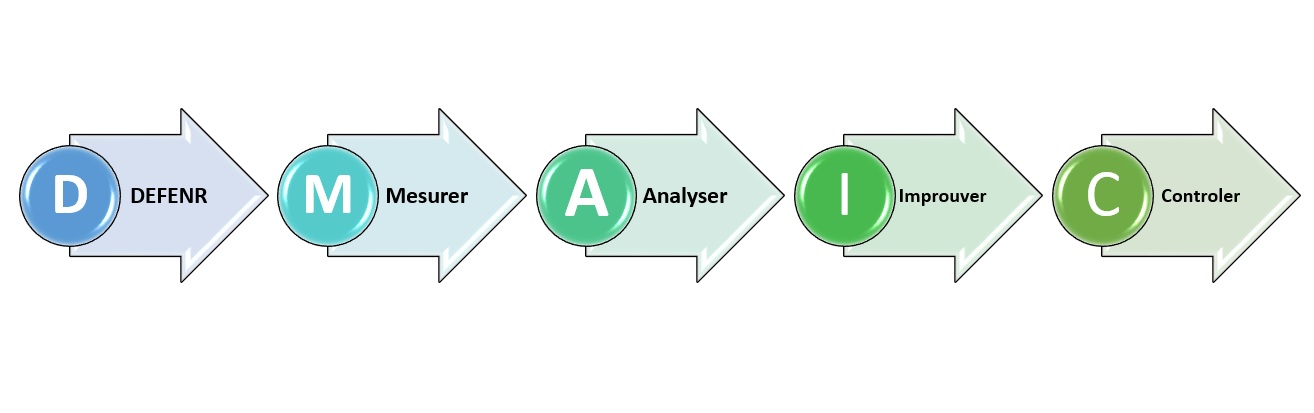
Mesurer Cette phase, qui consiste à recueillir des données dans le but de caractériser le procédé
Analyser identifier les causes induisant les dysfonctionnements étudiés, reconnaître les causes initiales (ou causes profondes) à l’origine de la problématique, afin de travailler sur les vrais problèmes plutôt que sur les symptômes qu’ils révèlent.
Improuver proposer des solutions en vue de répondre aux causes identifiées lors de la phase précédente,établir un plan d’action etmettre en place les solutions sélectionnées.
Contrôler La dernière étape du DMAIC est la phase de prise de recul par rapport au projet afin de contrôler que les modifications implémentées ont eu les effets escomptés. Communiquer sur le projet qui vient d’être mené et faire le bilan du projet afin de le clôturer .
SMED
Le SMED est né en 1970 dans l’univers industriel compétitif de TOYOTA, c’est l'abréviation de l'anglais Single Minute Exchange of Die(s), littéralement « changement rapide d’outil »
C’est une méthode qui cherche à réduire le temps de changement de série avec un objectif quantifié.

Analyser
Identification des réglages.Le but est d'identifier toutes les opérations réalisées lors de ce changement. Identifier: les opérations
internes et externes.
Dissocier la séparation entre les opérations "internes" et les operations "externes", les opérations externes (ils correspondent à des opérations qui se font lorsque la machine est arrêtée) et les opérations internes (ils correspondent à des opérations qui se font lorsque la machine est en fonctionnement). Le but de cette étape consiste à effectuer un
maximum d'actions tant que la machine travaille sur l'ancienne série.
Convertir
Cette phase consiste en la transformation d'opérations internes en opérations externes. Il en résulte une réduction du nombre
d'opérations internes et un gain global de temps. Cette étape implique en général un
investissement.
Réduire
C’est la réduction du temps d'exécution des opérations, tant internes qu'externes, par
leur rationalisation. Cette étape est consacrée à la recherche de simultanéité de tâches, Ã
l'optimisation de celles-ci ainsi qu'à l'amélioration des réglages en vue de la diminution du
nombre de pièces d'essais.
PDCA
L’amélioration continue repose sur la méthode PDCA représentée par la roue de Deming. Elle est divisée en quatre étapes.

Plan/Planifier définir les objectifs, choisir la démarche pour les atteindre et construire l’échéancier.
Do / Faire exécuter le travail qui a été prévu .
Check /Vérifier s’assurer que les objectifs visés sont atteints, sinon mesurer l’écart et interpréter.
Act /Corriger prendre les mesures correctives pour parvenir au résultat escompté.
Six Sigma
Le Six Sigma est une philosophie d’amélioration de la qualité qui préfère la prévention des défauts plutôt que leur détection. Cela passe par la fiabilisation des processus afin de les rendre stables, prévisibles et reproductibles.Travail en équipe assignation à des groupes de personnes de projets clairement définis et qui ont un impact certain sur la qualité des produits.
Formation à l’outil statistique pour tous cela permet également de mettre en avant des personnes ayant une compréhension accrue de la méthode et des compétences dans le management de projet, et qui pourront encadrer une équipe de projet.
Utilisation de l’approche DMAIC dans la résolution de problème.
Support de la part de l’encadrement pour fonctionner, le Six Sigma doit être une stratégie d’entreprise clairement établie.
Kaizen
Un outil indispensable mis en oeuvre dans le Lean Manufacturing est le Kaizen, mot japonais signifiant « amélioration continue ». Ce concept est basé sur de petites améliorations faites au quotidien, n’induisant pas ou peu d’investissements, et impliquant tous les opérateurs dans la recherche continue de l’atteinte des objectifs.
Value Stream Mapping (VSM)
La Value Stream Mapping (ou Cartographie de la Chaîne de Valeur) est un des outils du Lean Manufacturing. Elle est largement utilisée pour représenter les procédés et réfléchir à de nouvelles organisations réduisant les gaspillages.
0 Comments